In the modern era of recycling and waste management, the Plastic Color Sorting Machine and Plastic Polymer Sorter have emerged as essential tools in improving efficiency and accuracy in the sorting process. These machines play a crucial role in separating various types of plastic materials based on their colors and polymer types, leading to better recycling outcomes. Whether it’s distinguishing between PET and non-PET materials, or sorting HDPE, PP, PVC, and other polymers, these machines have become indispensable in industries that deal with plastic recycling.
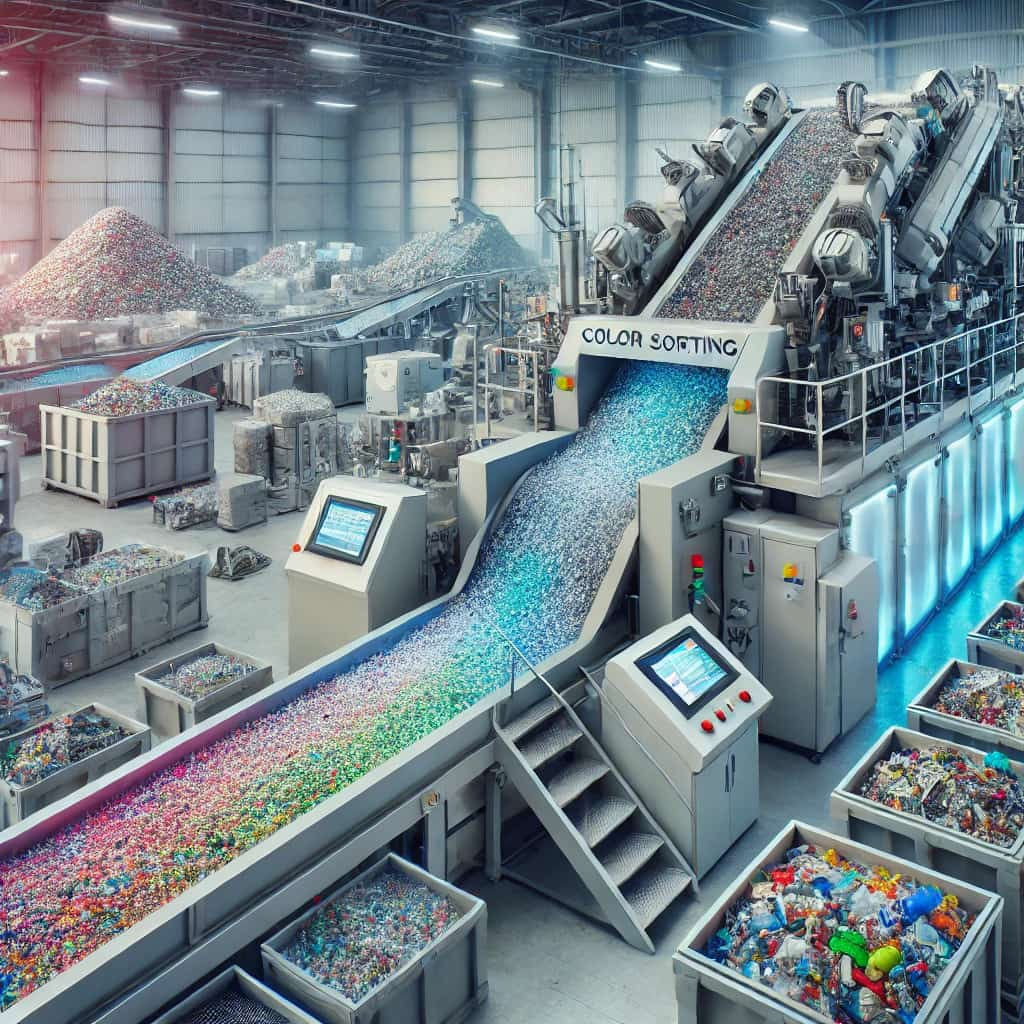
Key Features of Plastic Color Sorting Machines
Plastic color sorting machines are built with advanced technology designed to identify and differentiate between different types of plastics. The following are some of the most important features:
1. High-Precision Optical Sensors:
These machines are equipped with sophisticated optical sensors capable of detecting subtle differences in plastic materials based on color, transparency, and chemical composition. This precision ensures that even plastics with similar visual characteristics, such as HDPE and PP, can be accurately sorted.
2. Automated Processing:
Unlike traditional manual sorting, which is labor-intensive and prone to human error, plastic color sorting machines use automation to process large volumes of plastic quickly and accurately. This not only speeds up the sorting process but also reduces labor costs and increases efficiency.
3. Multi-Stream Sorting:
Some machines are capable of sorting multiple types of plastics in a single pass, differentiating between PET, HDPE, PVC, PP, and more. This versatility makes them suitable for use in recycling facilities dealing with mixed plastic waste streams.
4. Customization and Adjustability:
Plastic color sorting machines can often be customized or adjusted to suit the specific needs of a recycling plant. Whether it’s sorting by color, polymer type, or transparency, users can program the machine to focus on specific materials or grades, ensuring optimal recovery rates.
5. Energy Efficiency:
Modern plastic sorting machines are designed to minimize energy consumption, using smart technology to optimize operations. This reduces operational costs and lowers the environmental impact, making them more sustainable over the long term.
The Benefits of Using a Plastic Color Sorting Machine
Implementing a plastic color sorting machine in the recycling process offers several substantial benefits:
1. Improved Sorting Accuracy
Perhaps the most significant advantage is the increase in sorting accuracy. Manual sorting often leads to mistakes, as different types of plastics can be difficult to distinguish by eye. Optical sorting technology, however, uses sensors to identify even minute differences in color and material composition, ensuring a higher degree of precision.
For example, in recycling facilities that process beverage bottles, PET and HDPE bottles often get mixed together. A plastic sorting machine can easily distinguish between these two materials based on their color and physical properties, separating them for more effective recycling.
2. Increased Efficiency and Throughput
Plastic sorting machines significantly increase the speed at which materials can be processed. Human workers might be able to sort a few hundred kilograms of plastic per day, but automated machines can process several tons of plastic in the same amount of time. This increased throughput allows recycling facilities to handle higher volumes of waste, leading to greater profitability and a larger positive impact on the environment.
In practice, a plastic sorting machine can handle complex waste streams, such as post-consumer plastic from households or industrial packaging waste. For example, a facility tasked with recycling automotive plastics will face a wide variety of plastic types, from ABS to PP. A plastic color sorting machine will help sort these materials faster and more efficiently than manual methods ever could.
3. Reduction in Labor Costs
One of the key economic advantages of using a plastic sorting machine is the reduction in labor costs. Since the machine performs much of the work automatically, fewer staff members are needed to oversee the sorting process. This frees up workers to focus on other tasks, reducing overall costs for the recycling facility.
Moreover, automation reduces the risk of injury associated with manual sorting, as workers are no longer exposed to hazardous materials or repetitive strain injuries caused by sorting large volumes of plastic by hand.
4. Higher Quality Recycled Plastic
By improving sorting accuracy, plastic sorting machines contribute to producing higher-quality recycled plastic. When different types of plastic are mixed together, the quality of the recycled material is compromised, limiting its use in new products. For instance, if PVC is mixed with PET, the resulting recycled material may not meet the standards required for food-grade packaging or other high-value applications.
With a plastic color sorting machine, plastics are sorted more accurately, resulting in purer batches of material that can be used to create higher-quality recycled products. This improves the value of the recycled material and increases the overall sustainability of the recycling process.
5. Environmental Impact
Effective sorting not only leads to better recycling outcomes but also helps reduce environmental harm. By properly sorting plastics, recycling plants can divert more materials from landfills, reducing pollution and conserving resources. Furthermore, improved recycling rates help reduce the need for virgin plastic production, which is associated with high energy use and greenhouse gas emissions.
Use Cases of Plastic Sorting Machines
1. PET Bottle Recycling:
In many countries, recycling centers deal with vast quantities of plastic bottles, primarily made from PET. Sorting PET bottles from other types of plastic, such as HDPE, is crucial to maintaining the quality of recycled plastic. The introduction of plastic color sorting machines has improved the efficiency of PET recycling by automatically separating PET from other materials like caps, labels, and different polymers.
2. E-Waste Recycling:
In the electronics industry, e-waste recycling involves handling a complex mix of plastics, metals, and other materials. Plastic sorting machines can distinguish between different types of plastic found in electronic devices, such as ABS and PC, making it easier to recycle these materials effectively.
3. Mixed Plastic Waste Management:
Municipal recycling facilities often receive mixed plastic waste from households, which may include a variety of plastics such as PVC, PP, and HDPE. Plastic color sorting machines help efficiently process these waste streams, reducing contamination and ensuring that each type of plastic is properly recycled.
Real-World Case Study: European Plastic Recycling Facility
A European plastic recycling facility recently installed an advanced plastic color sorting machine to handle mixed plastic waste from packaging. The machine was programmed to differentiate between PP, HDPE, and PET plastics. Since its installation, the facility has seen a significant improvement in its sorting efficiency, processing up to 30% more material each day while reducing contamination rates by 25%.
By automating the sorting process, the facility has also been able to reduce its labor costs by 15%, while the quality of the recycled plastic has improved to the point that the company now supplies higher-grade recycled materials to the automotive and consumer goods industries.
Plastic color sorting machines have revolutionized the recycling industry by increasing accuracy, efficiency, and the quality of recycled materials. From separating PET bottles to handling complex e-waste streams, these machines provide a practical solution to one of the most pressing challenges in modern recycling. They reduce the need for manual labor, improve the purity of recycled plastics, and contribute to more sustainable waste management practices. As recycling efforts continue to expand worldwide, the adoption of plastic sorting machines is set to play an increasingly vital role in creating a circular economy for plastics.