Introduction
Originally manually driven instruments used to form materials by use of rotary cutters, traditional milling machines For years, they have been pillar of production as they provide dependability and adaptability. For particular jobs, the hands-on experience these machines provide—allows the operator to directly control the movement of the cutting tool—is priceless. Their design calls for a table for the workpiece, a spindle for the cutting tool, and handwheels or levers to accurately guide motions. Depending on the spindle's position, traditional milling machines are sometimes classified as horizontal or vertical mills.
CNC machining shapes, cuts, finishes materials using computer-operated, automated techniques. Operating on pre-programmed designs, the CNC technology guarantees repeatability and accuracy, unlike hand milling. Modern software lets CNC machines tackle difficult geometries and sophisticated designs. Usually comprising a computer interface, many axes of movement (including X, Y, and Z axes), and different tool attachments for drilling, cutting, and shaping.
Each of conventional milling and CNC machining has special advantages and drawbacks. While CNC machines provide scale and accuracy, traditional mills stress workmanship and adaptability. Whether for specialized one-off items or mass production runs, producers may better match their expenditures with project objectives by evaluating these technologies.
This comparison also emphasizes how improvements in technology affect manufacturing quality and efficiency.
Overview of Traditional Milling Machines
Mechanics and Operation
Conventional milling machines run on human effort. Handwheels and levers allow the machinist to move the workpiece and cutting tool, therefore personally managing every element of the machining process. Though they run on somewhat simple ideas, these devices require great knowledge to get excellent outcomes.
To guarantee accuracy, the machinist must hand change the cutting tool's speed, depth, and feed rate. This practical approach makes conventional mills especially helpful for smaller tasks or those needing constant changes.
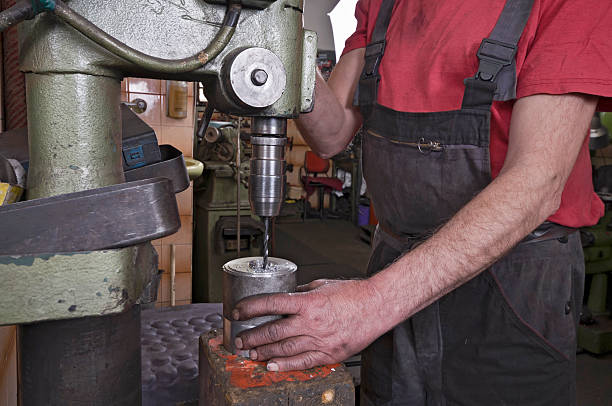
Common Applications
● For first models and testing ideas, traditional mills are perfect. Machinists may quickly iterate by making on-demand changes made possible by hand control.
● Manual milling machines are commonly used in small workshops and by artists to create unique, handcrafted designs or one-of- a-kind components.
● Traditional mills provide reasonably priced solutions without requiring significant programming or setup time for limited run of components..
Advantages
● Generally speaking, traditional milling machines demand less starting investment than their CNC equivalents. Their lower maintenance needs help to lower long-term running expenses as well.
● For unusual or non-repetitive jobs, conventional mills are perfect because of quick setup and adaptability midway through the process.
● Using their knowledge and the manual controls on the machine, skilled machinists can produce complex designs. This enables imagination and problem-solving not possible in automated systems.
Limitations
● Human ability and potential tiredness define the precision of conventional milling intrinsically. Getting consistent results over several sections might be difficult.
● Manual operation requires more time, hence conventional mills are less suited for high- volume or repeated work.
● Operating classic milling machines efficiently calls for a significant degree of expertise and experience.
Overview of CNC Machines
Mechanics and Operation
To automate the milling process, CNC machines depend on sophisticated programming. Designs entered into software by operators create G-code, the language running the machine. Usually incorporating X, Y, Z, and even rotating axes for complicated designs. These directions control the movement of the cutting tool over several axes.
Many sensors and feedback systems included into CNC machines guarantee exact command execution. This automation reduces human mistake and makes consistent output possible.
Common Applications
● The backbone of sectors like electronics and automobiles that demand large-scale manufacture is CNC machines. Their unequaled capacity to create exact components on mass is
● CNC machining provides the accuracy required for important components in sectors including aerospace and medical manufacture. Two examples are orthopedic implants and turbine blades.
● Creating complex forms and multi-axis designs difficult or impossible with hand milling is something CNC machines excel at. For complex engineering projects and prototypes, this capacity is very vital..
Advantages
● Far beyond the limits of hand milling, CNC machines may get tolerances as close to ±0.001 inches.
● Even with difficult designs, automation drastically lowers manufacturing times. Once programmed, CNC machines may run constantly under little direction.
● Every component generated is exactly the same as the last guarantees consistency in large volume manufacturing cycles.
● Mostly concerned with setup and monitoring, operators help to lessen the need for highly qualified machinists.
Limitations
● Purchasing and configuring CNC machines comes with a large initial cost that usually calls for large money.
● Precision mechanical and electrical systems used in CNC machines call for specific skills for maintenance and repairs.
● To build and maximize machining programs, operators must be knowledgeable in CAD (Computer-Aided Design) and CAM (Computer-Aided Manufacturing). For smaller companies or less seasoned teams, this learning curve might provide challenges.
Key Differences Between Traditional Milling and CNC Machines
Control Mechanisms
Manual Control in Traditional Milling
Dependant on handwheels and levers to guide the cutting tool, traditional milling machines place control straight in the hands of the machinist. This practical technique provides the degree of adaptability needed for real-time machining process corrections.
Traditional milling is a great fit for bespoke, low-volume jobs or prototypes as operators may adjust on demand to accommodate changes in material, design, or other unanticipated conditions. But human capacity naturally limits the accuracy attainable with hand control.
Maintaining consistency across several sections can be difficult as little differences in movement or alignment could result in differences in the final output. This reliance on operator ability highlights the importance of competent machinists producing excellent output.
Automated Control in CNC Machining
Through pre-programmed instructions, CNC (Computer Numerical Control) machines automate the milling process, therefore transforming production. Following CAD/CAM-generated code to direct the cutting tool across several axes, these machines precisely and consistently complete jobs.
This guarantees consistency in high-volume production and removes the need for continuous human interaction, therefore lowering the possibility of mistakes.
CNC machines offer allow for handling complicated designs and precise geometries that would be challenging or impossible to do manually thanks to automation. For sectors including aerospace, medical devices, and automotive components needing strict tolerances, CNC machining is perfect with increased precision and repeatability.
Although the first programming step calls for technical knowledge, CNC is a pillar of contemporary manufacturing because its long-term advantages in production and quality.
Precision and Accuracy
● Traditional Milling: Achieving tight tolerances depends heavily on the skill of the operator. While experienced machinists can produce precise work, consistency across multiple parts is challenging.
● CNC Machines: Capable of achieving microscopic tolerances with unmatched consistency, CNC machining is the standard for high-precision applications.
Speed and Production Volume
● Traditional Milling: Manual operation is inherently slower, making it suitable for low-volume production or unique, custom parts.
● CNC Machines: Designed for speed and efficiency, CNC machines can handle large production runs with ease. Their ability to operate continuously further enhances productivity.
Complexity of Design
● Traditional Milling: Best suited for simpler geometries or designs where adjustments are made during the machining process.
● CNC Machines: Handles intricate, multi-axis designs with precision, making them indispensable for advanced engineering and prototyping.
Skill Requirements
● Traditional Milling: Requires hands-on craftsmanship and years of experience to master. Operators must understand the machine’s mechanics and possess strong problem-solving skills.
● CNC Machines: While less dependent on manual dexterity, CNC operation demands proficiency in programming and software. Training in CAD/CAM tools is essential for creating effective machining programs.
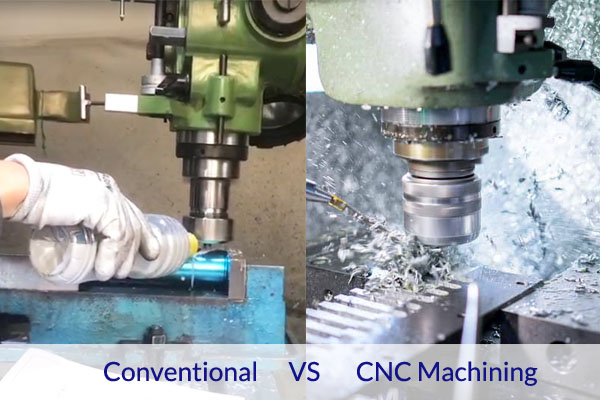
Cost Analysis
Choosing between conventional milling and CNC machines has major cost consequences depending on numerous aspects including the size of production, required accuracy, and long-term operational goals.
Initial Investment
Depending on the brand, size, and features, traditional milling machines usually cost less initially—between $5,000 and $30,000. Smaller workshops or startups with tighter resources can use these devices.
On the other hand, CNC machines are a big investment; entry-level versions start at $50,000 and powerful multi-axis systems top $500,000.
Since this first outlay usually consists of software, extra tools, and setup expenses, CNC machines represent a more reasonable financial commitment.
Operational Costs
Although conventional mills have less running costs, their labor-intensive nature makes Higher labor expenses result from skilled machinists operating and adjusting the machines personally.
These machines have less complicated components, hence maintenance is easier and less costly.
Conversely, because of their complexity, CNC machines have greater continuous expenses. They use more power, and upkeep calls for certain experts. Add to the total cost are tool replacements, programming, and software upgrades.
But for high- volume manufacturing runs especially, quicker production times and lower labor costs frequently balance these operating expenses.
Return on Investment (ROI)
Given its cheaper purchase and maintenance costs, conventional mills often offer a faster ROI for low- volume or specialized applications. But CNC machines are more appropriate for sectors where scalability, speed, and accuracy rule most importantly.
Faster ROI in large-scale operations depends on the capacity to create identical components with less waste.
Advantages of Combining Both Technologies
Flexibility in Production
Blending CNC machining and classical milling in a production setting lets companies optimize their capabilities. For rapid changes, one-of-a-kind projects, or prototype building, traditional mills are perfect. On the other hand, CNC machines shine at creating intricate, high-precision parts at scale.
Optimized Resource Utilization
These technologies taken together guarantee the best use of resources. For example, whereas conventional mills may concentrate on smaller work, CNC machines can manage complex or large-scale tasks. Therefore decreasing bottlenecks and raising general efficiency.
Enhanced Production Capabilities
The advantages of both systems can help producers satisfy a wider spectrum of projects. From complex designs calling for automation to unique, handcrafted components demanding a human touch, the dual approach addresses many consumer wants.
Cost Management
Although keeping two kinds of gear entails more initial expenses, using each system for jobs where it shines helps to balance the total expenses.
This separation guarantees that conventional mills stay operational without overloading them and helps to minimize wear and tear on CNC machines.
Case Study
Imagine a mid-sized workshop including CNC machinery in addition to conventional mills. Within the first year, they lowered CNC machine downtime by 20% and raised general production efficiency by 30% by employing conventional milling for easier tasks and auxiliary procedures.
Future Trends in Milling and CNC Technology
In the realm of milling and CNC technologies, change is happening fast. Technological developments redefining our approach to manufacturing are shaping machining's future as sectors push for greater precision, higher production, and sustainable practices.
Among the most notable developments are improvements in automation, the rise in hybrid vehicles, more affordability, and environmental concerns.
Advancements in Automation
Among the most transforming features of contemporary CNC technology is automation. While traditional milling machines needed continuous human intervention, CNC machines have allowed greater efficiency and productivity with little manual input.
To maximize their operations, CNC machines are growing smarter today by including artificial intelligence (AI) and machine learning techniques.
By means of real-time adjustments based on data received, artificial intelligence enables CNC machines to improve accuracy and efficiency. Machine learning, for example, can enable tools to be predicted or even machining parameters to guarantee consistency over a production run.
These developments are enabling CNC machines to be even more autonomous, so lowering the need for human intervention and increasing production in sectors including aerospace, automotive, and medical device manufacture.
Hybrid Machines
The development of hybrid machines combining the accuracy of CNC technology with the adaptability of hand milling is another important trend. These devices enable producers to perform complex tasks with exceptional precision, while also enabling manual intervention when necessary, thereby combining the advantages of both technologies.
Combining conventional subtractive machining with additive manufacturing (3D printing) hybrid machines provides a flexible answer for sectors using both methods.
Manufacturers that must promptly and effectively transition between many processes and find the rising appeal of hybrid machines, particularly in sectors with fast changing designs and production requirements.
Affordability and Accessibility
CNC technology's accessibility and cost have witnessed notable advancements. CNC machines were seen in the past as very costly and complicated for amateurs and small enterprises. But because to technological developments, desktop CNC machines—which are now within reach for small-scale companies and individual creators—have emerged.
On a range of materials, including metals, plastics, and wood, these smaller, more reasonably priced machines may execute precision work. CNC technology's increasing availability creates opportunities for innovation and creativity in sectors traditionally exclusive to major enterprises.
Custom fabrication, prototyping, and low-volume production made possible by this technology let hobbyists, small enterprises, and educational institutions benefit.
Environmental Considerations
The CNC sector is also emphasizing lessening its environmental effect as the need for sustainability rises. Modern CNC machines have technology that lower power consumption and cut waste, therefore considering energy efficiency in design.
These machines consume less energy while preserving high degrees of performance by streamlining machining techniques.
Another main emphasis area is the decrease of material waste. Higher material consumption made possible by advanced CNC systems guarantees that every bit of the material is used effectively.
Moreover, developments in recycling technology let producers turn metal waste into valuable goods, therefore lowering the total environmental effect.
Conclusion
The comparison between conventional milling and CNC technology reveals different benefits and uses for both, therefore providing companies and producers with insightful analysis of their relative possibilities. With flexibility at a cheaper cost, traditional milling is still a dependable option for small-scale operations, prototyping, and handcrafted work.
On the other hand, CNC machines are the preferred choice for difficult jobs requiring accuracy and efficiency as well as for big volume manufacturing as they shine in precision, speed, and scalability.
The particular requirements of the company will eventually determine whether conventional milling or CNC technology is more suited. For businesses that give low-cost, low-volume, or customized manufacturing first priority, conventional milling provides a versatile method. CNC machines, which may simplify manufacturing and lower human error, thereby benefiting companies needing large-scale, exact, repeatable operations will help to increase consistency and output.
The future of milling and CNC technologies seems to be bright. The manufacturing scene is changing significantly as automation continues to grow, hybrid machines become more common, affordability rises, and sustainability takes front stage.
These developments not only promise to increase output but also enable amateurs and small companies to use CNC technology's capability.
Businesses who want to remain competitive and flourish in a constantly changing industry will have to keep updated about these trends and adjust to new technology.