FLANNEL
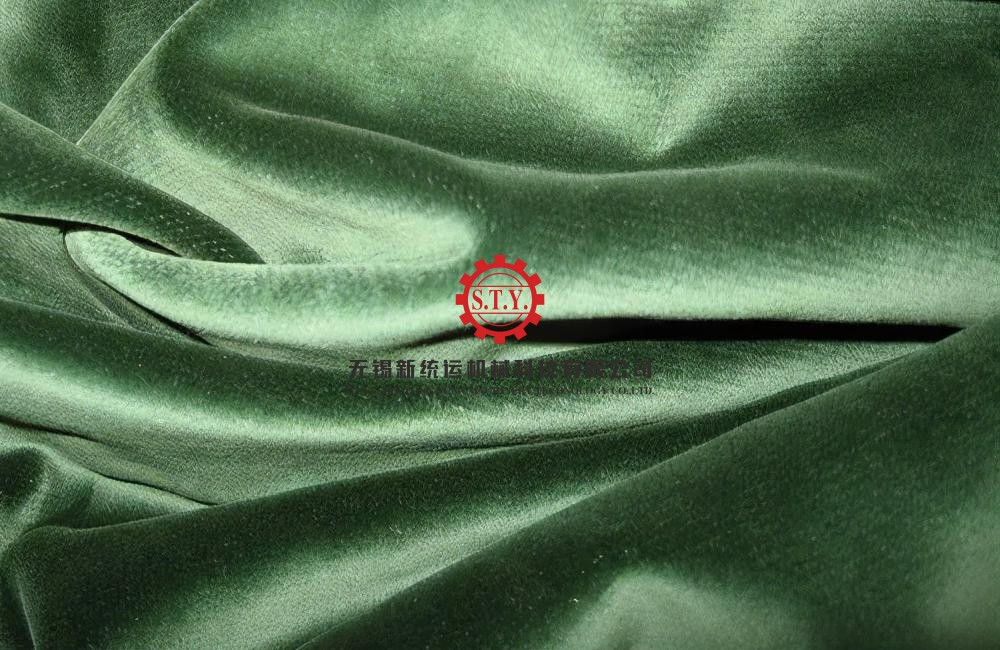
Material:Originally made of wool, now also available in polyester and other synthetic fibers as imitation flannel.
Appearance & Feel: Short and dense fine hairs, tightly structured, resistant to deformation, good gloss, and soft to the touch.
Properties: Excellent moisture absorption and breathability, strong insulation, and minimal shedding.
Applications: Commonly used in suits, trousers, bedding, etc.
CORAL FLEECE
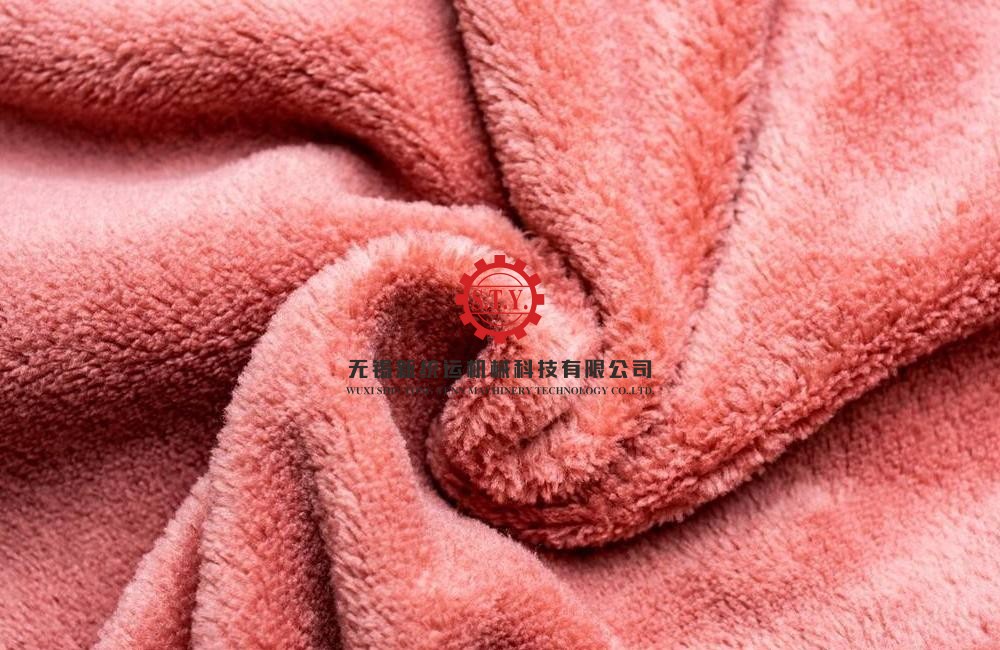
Material: Made of polyester fibers.
Appearance & Feel: Long and dense hairs resembling the soft body of live coral, colorful, and soft to the touch.
Properties: Good insulation, but the longer the hairs, the poorer the moisture wicking ability; not prone to pilling but prone to shedding.
Applications: Often used in making robes, pajamas, baby products, children's clothing, footwear, hats, toys, etc.
POLAR FLEECE
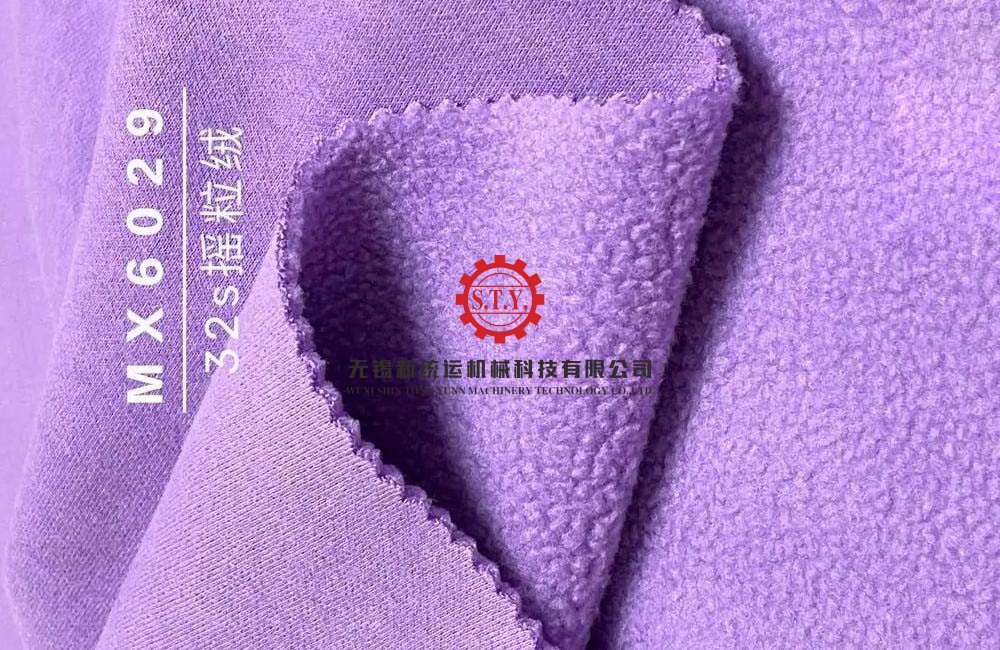
Material: Generally made of polyester fabric, with the option to add a certain percentage of spandex (which can be difficult to control in quality).
Appearance & Feel: The front side has fluffy and dense loops, while the back side has sparse and uniform loops with short hairs, feeling soft to the touch.
Properties: Elastic, insulating, wear-resistant, non-shedding, mold-resistant, moth-proof, good elasticity, and resistant to wrinkles and deformation.
Applications: Commonly used in outerwear, children's clothing, hoodies, cold-weather outerwear, loungewear, etc.
POLYESTER SHERPA
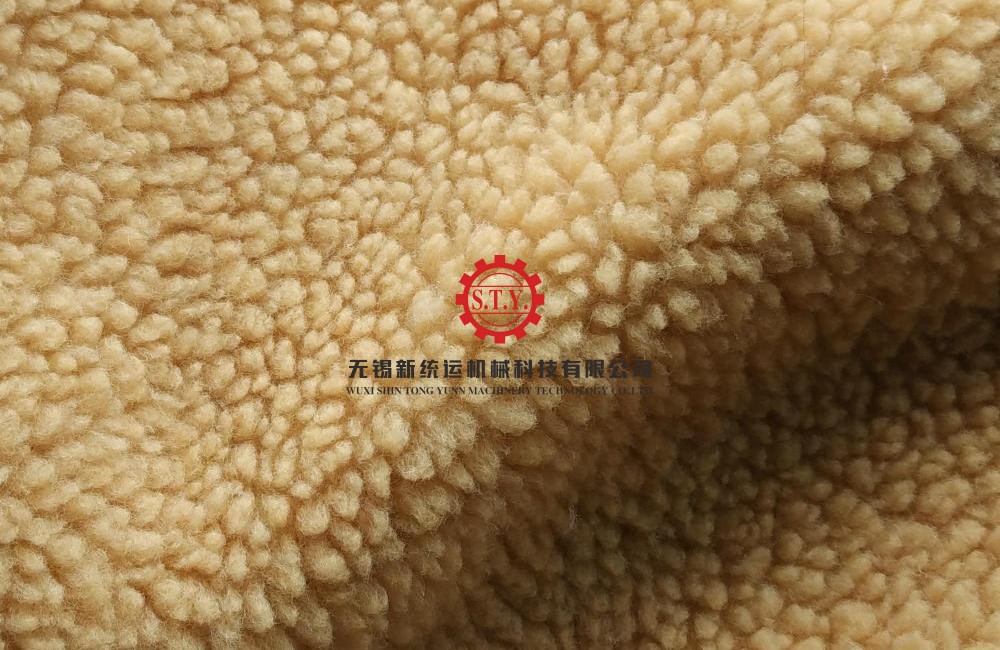
Material: Synthetic fabric made of pure polyester or blend of polyester and acrylic fiber.
Appearance & Feel: Relatively long and fluffy hairs resembling lamb's wool, feeling soft to the touch.
Properties: Wear-resistant, mold-resistant, moth-proof, good elasticity, and resistant to wrinkles and deformation.
Applications: Often used in making outerwear, loungewear, hats, toys, etc.
MILK FLEECE
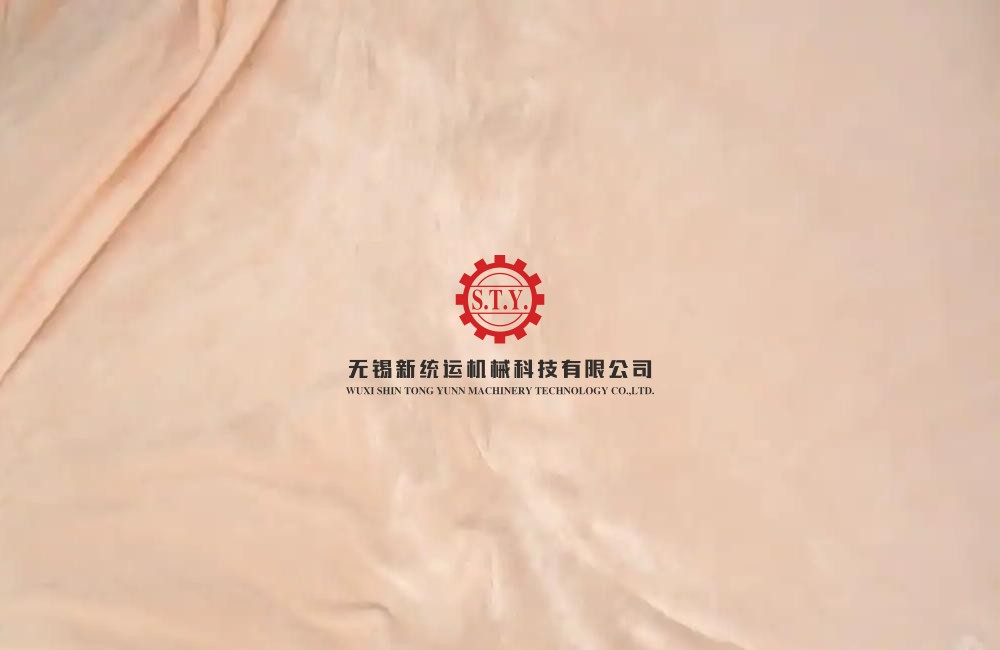
Material: A new type of animal protein fiber made from milk as the basic raw material, after dehydration, degreasing, purification, and blending, crosslinking, and grafting with polyacrylonitrile.
Appearance & Feel: Short and dense hairs, treated for softness, silky smooth like milk, good gloss, and soft to the touch.
Properties: Excellent moisture absorption and breathability, strong insulation.
Applications: Commonly used in bedding, high-end underwear, etc.
VELVET
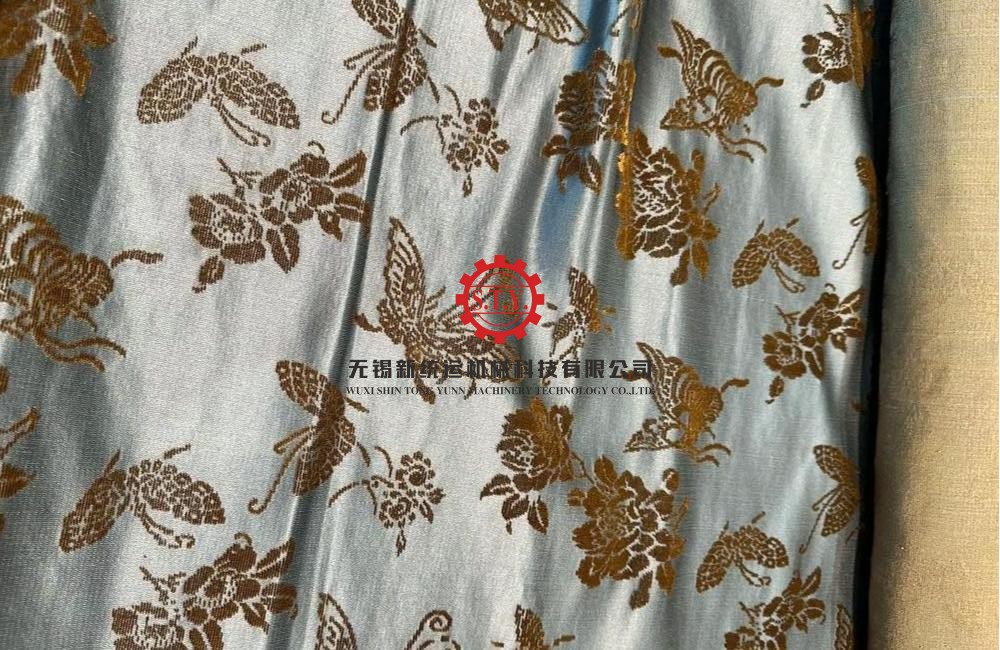
Material: Silk fabric woven with silk or artificial silk loops and cotton yarn as the weft.
Appearance & Feel: Luxurious and elegant appearance, dense pile hairs, long and slightly inclined, silky smooth to the touch.
Properties: Good insulation, bright gloss.
Applications: Can be used to make autumn and winter clothing, hats, silk velvet blankets, and decorations, as well as high-end sofa covers, curtains, etc.
These fabric can be dyed by TY-JL636 series high temperature high pressure low tension fabric dyeing machine, according the width and GSM fabric can be adjusted the nozzle size.