CNC machines are an important part of custom manufacturing and machining, but they aren't all the same. Two of the most common types are CNC lathes and CNC mills. While both rely on computer-controlled systems to shape materials with precision, they work in different ways.
A CNC lathe rotates the material against a stationary cutting tool, while a CNC mill rotates the cutting tools around a fixed piece. Each machine has its own strengths and is better suited for specific tasks. Understanding the differences between them will help you choose the right tool, improve efficiency, and get the best results for your project.
This guide will break down what each machine does, how CNC lathe works, and why knowing the difference between CNC machine vs CNC lathe can save you time and improve your results.
Importance of Understanding the Differences Between CNC Machines and CNC Lathes
Understanding the difference between CNC machine vs CNC lathes is important for making the right choices in any machining or fabrication project. Both machines handle tasks differently, and knowing when to use each one can greatly impact the outcome of your work. Here are a few key reasons why understanding these differences is so important:
• Choosing the correct machine helps the project flow smoothly and produce the best results, especially for specific shapes or more complex designs.
• Selecting the appropriate machine helps avoid unnecessary expenses caused by slower production times, material waste, or tool wear.
• Each machine is suited for specific tasks, so using the proper one leads to more accurate and effective outcomes.
• With the right machine, you can cut down production time and avoid delays caused by switching or redoing tasks.
By understanding these differences, you can make smarter decisions, improve workflows, and reduce costs on any project. This knowledge helps you maximize your resources and achieve high-quality results from the beginning.
What is a CNC Machine?
A CNC (Computer Numerical Control) machine is automated equipment that shapes materials like metal, wood, or plastic. The machine follows a pre-programmed set of instructions, guiding the cutting tools to work on the material as required. This automation results in highly detailed work without needing manual control, making CNC machines essential in modern production.
Types of CNC Machines
There are several types of CNC machines, each suited to different tasks:
• Milling machines: These machines move rotating cutting tools across materials to carve or drill. They excel at producing complex shapes and detailed parts.
• Routers: CNC routers cut materials like wood or plastic and are commonly used in industries like cabinetry or sign-making.
• Plasma cutters: Using a plasma torch, these machines cut through conductive materials such as steel or aluminum, making them popular in metal fabrication and automotive industries.
• Lathes: CNC lathes rotate the material while stationary cutting tools shape it. They are ideal for creating parts like shafts and screws.
Key Applications and Industries
CNC machines are widely used across many industries due to their ability to perform repetitive and detailed tasks. Some common applications include:
• Automotive: Used to produce car parts like gears, engine parts, and other detailed pieces.
• Aerospace: These machines create lightweight, complex parts required for aircraft and spacecraft.
• Manufacturing: CNC machines produce a variety of custom tools and instruments used in different sectors.
• Construction: CNC technology shapes building materials, including metal beams and panels, to exact specifications.
CNC machines provide automated, highly consistent results across a range of industries. From aerospace to construction, they make detailed parts efficiently. Understanding the different types of CNC machines and their applications can help you make informed choices that benefit your projects and lead to better overall outcomes.
What is a CNC Lathe?
A CNC lathe is a machine used to shape materials by rotating the workpiece while a stationary cutting tool removes material. It’s specifically designed for jobs that require symmetry, such as pipes, bolts, or tubes. CNC lathe operation are highly versatile, able to handle a range of materials, and are known for their efficiency in producing large quantities of uniform parts.
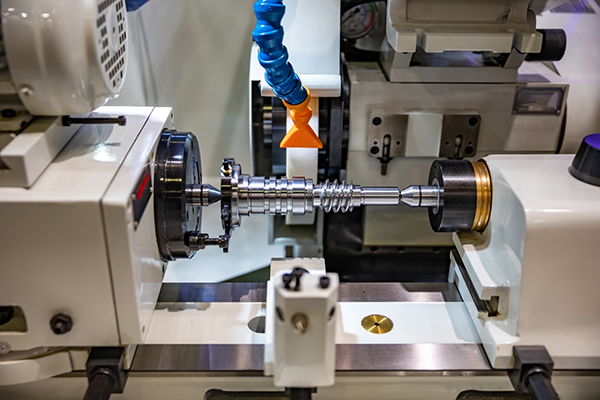
Main Parts of a CNC Lathe
A CNC lathe operation consists of several key components that work together to shape the material with precision. Understanding these main parts can help you see how the machine operates and why it’s effective for certain tasks:
• Spindle: This part is responsible for rotating the workpiece. The spindle’s speed can vary depending on the material and the type of cut being made.
• Chuck: The chuck acts as a clamp, holding the material securely in place during rotation. It adjusts to fit different sizes of workpieces.
• Turret: The turret holds several different cutting tools, allowing the machine to switch tools automatically during the process. This makes CNC lathes efficient at performing multiple operations, like cutting, drilling, or grooving, without stopping.
Common Materials and Parts Processed on CNC Lathes
In some situations, CNC lathes can also handle plastics and even wood in addition to a range of materials, including several kinds of metals, such steel, aluminum, and brass. The machine's flexibility lets it generate numerous parts, including:
• Screws: Perfectly round and uniform threads for fasteners.
• Shafts: Long, tubular components used in engines or machinery.
• Bushings: Rings that reduce friction in mechanical systems.
• Fittings and connectors: Used in plumbing, automotive, and aerospace applications.
These parts are commonly used in industries where precision and repeatability are key, like automotive manufacturing, aerospace engineering, and even medical device production.
Key Differences Between CNC Machines and CNC Lathes
CNC lathes and CNC machines are indispensable instruments for modern manufacturing, each providing unique capabilities. Both machines use computer code to automate tasks, but the way they work, how they handle materials, and what other features they have can have a big effect on how a project turns out. To select the ideal machinery for your unique requirements and to get the greatest results, you must understand the difference between CNC machine and CNC lathe.
Aspect
|
CNC Machines
|
CNC Lathes
|
Type of Motion
|
Uses multiple axes (3, 4, or 5) to control the cutting tool’s movement. The workpiece remains stationary while the tool moves, allowing for detailed shapes.
|
Rotates the workpiece while the cutting tool remains stationary. Best for producing rodlike or round parts like shafts and pipes.
|
Materials and Shapes Processed
|
Can handle various materials like metals, plastics, and wood. Creates intricate shapes, flat surfaces, and deep cuts, ideal for custom parts.
|
Specialized for rotationally symmetrical objects such as conical, and spherical shapes. Best suited for shaping metals like steel, aluminum, and brass.
|
Tooling and Detail Work
|
Uses multi-point cutting tools such as end mills or face mills for intricate designs. Perfect for projects requiring varied cuts or multi-operation tasks.
|
Relies on single-point cutting tools for turning operations. Best for shaping round surfaces, but limited in internal details.
|
Operational Method
|
Commonly used for milling, drilling, and cutting. The tool moves around the stationary workpiece, creating complex designs and detailed shapes.
|
Uses a turning method where the workpiece rotates. Ideal for producing symmetrical parts quickly and consistently.
|
Performance Factors
|
Excellent for handling multi-step operations and intricate designs, but setup times can be longer. Suitable for varied materials and complex tasks.
|
Highly efficient for producing axial parts quickly. Best for high-volume production of identical, round components.
|
Advantages
|
Versatile in handling multiple machining operations and materials. Ideal for custom designs and projects requiring precision.
|
Best suited for mass production of parts. Fast and reliable for repetitive tasks.
|
Limitations
|
Slower for high-volume production and less suited for projects requiring symmetrical parts.
|
Limited in handling non-symmetrical designs or multi-step operations that require different cutting angles.
|
Real-World Applications
|
Used in aerospace, automotive, and medical industries for creating complex engine parts, molds, and custom tools.
|
Primarily used in automotive and manufacturing industries for producing shafts, screws, bushings, and other rounded pieces.
|
Beyond the surface-level difference between CNC machine and CNC lathe, CNC machines and CNC lathe operations diverge significantly in how they integrate into various manufacturing processes, handle different tasks, and meet industry-specific needs:
CNC Machines: Adaptability and Customization
CNC machines, such as mills, excel in projects requiring multiple steps like drilling, cutting, and milling, making them ideal for industries that need a variety of tasks and detailed customization, such as aerospace. These machines can handle different materials and intricate designs, though this capability can result in slower production speeds for large volumes.
CNC Lathes: Specialization and High-Volume Output
CNC lathes, on the other hand, focus on producing round parts like shafts, screws, and fittings. They are designed for high-volume, consistent output with minimal downtime, making them valuable for industries like automotive manufacturing. While CNC lathes may not offer the same range of motion or adaptability, they are highly effective at creating uniform parts quickly and efficiently.
Choosing the Right Machine for the Task
CNC machines are perfect for tasks requiring exact, detailed cuts, particularly in sectors like healthcare. However, for projects focused on producing pieces quickly and cost-effectively, CNC lathes are the better choice. Their streamlined process reduces setup time and operational costs, making them more suitable for high-output production lines. Ultimately, selecting the right machine depends on the specific task, material, and desired outcome.
When to Use a CNC Machine vs. a CNC Lathe
Selecting the right machine for your project leads to better results and smoother operations. CNC machines and CNC lathes excel at different tasks. Knowing the difference between CNC machine and CNC lathe, and when to use each one will help you choose the best one for the job and keep your production running smoothly.
When to Use a CNC Machine
CNC machines, such as mills and routers, work well for tasks that require detailed designs and multiple steps. Below are scenarios where CNC machines are the best choice:
For Detailed Shapes
CNC machines handle jobs that need intricate and varied designs. When a project includes features like grooves, pockets, or irregular shapes, CNC machines are great at cutting materials to match those needs. Their ability to work along different paths makes them ideal for creating parts with a lot of detail.
For Multi-step Projects
When a project involves several different machining steps, such as drilling, cutting, and milling, CNC machines perform these tasks without needing to reset the material. This setup makes them ideal for creating parts that require various types of cuts or operations in a single process.
For Flat Surfaces and Deep Cuts
CNC machines, especially mills, are designed to create flat surfaces or make deep cuts. They shape materials evenly, making them perfect for projects like molds or metal parts, where precise measurements and even surfaces are needed.
When to Use a CNC Lathe
CNC lathes work best for creating round or symmetrical parts. They are the top choice when a project requires shapes centered around a rotating axis. Below are examples of when CNC lathes shine:
For Round Parts
CNC lathes excel at creating round objects like shafts, pipes, or bolts. The spinning action of the lathe produces smooth, even results, making them perfect for parts that need to be cylindrical.
For Large Production Runs
CNC lathes are the go-to machines for producing large numbers of identical parts. They are excellent at making the same piece over and over, which is useful in industries that need consistent parts quickly. The speed and accuracy of CNC lathes make them a key tool for high-volume production.
For Simple, Symmetrical Designs
If a project requires parts that are symmetrical along a central axis, such as pulleys, bushings, or nozzles, CNC lathes are the best fit. Their design focuses on producing these shapes quickly and consistently.
CNC machines and CNC lathes each have strengths that suit different tasks. CNC machines work best for detailed designs and multi-step projects, while CNC lathes are perfect for creating cylindrical parts and handling large production runs. Choosing the right machine for your project helps you save time and produce high-quality results.
Conclusion
Each machine has its strengths, and choosing between a CNC machine and a CNC lathe depends on the specific parts you need to produce. If you’re working on intricate, multi-step designs, a CNC machine is ideal, offering flexibility and precision. However, if your project involves creating uniform, rotational parts like shafts or pipes, a CNC lathe is the better choice. The right selection isn’t just about the machine itself, but how well it fits the material and the specifics you want to achieve.