Factors affecting the glue coating effect of PUR hot melt glue machine
PUR hot melt adhesive (Polyurethane Reactive) is a new type of one-component, solvent-free hot-melt structural adhesive. It is cured by moisture in the air and has excellent bonding strength and impact resistance after complete curing. It also has With excellent bonding strength, temperature resistance, chemical corrosion resistance and aging resistance, it has become the best adhesive for bonding in electronic industries such as mobile phones in recent years.
Factors and solutions that affect the production process during the gluing process of the product:
1. Influence of chemical composition of PUR hot melt adhesive
The amount of certain chemical components of PUR hot melt adhesive directly affects the viscosity of PUR. From the perspective of product performance, we must choose a suitable glue.
2. The influence of different bonding materials
PUR hot melt adhesive has good bonding ability to different base materials, such as rubber, plastic, glass, metal, leather, wood, fabric, etc. For different bonding materials, choose the appropriate glue model.
3. The amount of glue applied
The amount of PUR adhesive layer applied will affect the curing time. If the adhesive layer is thin, the curing time will be short. When the amount of glue applied is large, the moisture content of the cured glue will be relatively insufficient, and the curing time will be longer, which will ultimately affect the bonding strength of the structural parts.
4. Dispensing opening time
The specific time for the PUR hot melt adhesive applied on the sample to be exposed to the air should be based on the parameters of the adhesive. Generally, within one minute or less, the composite bonding effect is optimal. Complete the bonding within the effective opening time to prevent the glue line from drying out due to too long opening time, resulting in poor wetting effect of the glue line and thus affecting the strength of the bond.
5. Pressing
The structural parts after assembly with PUR hot melt adhesive must be pressed together, the time should be no less than 15 seconds, and the pressure should be no less than 3 kg. The purpose is to make the glue form a good glue thickness and glue wetting effect between the two bonding surfaces.
6. Ambient temperature and humidity
PUR hot melt adhesive is cured by moisture in the air. If the ambient humidity is high, the curing time will be short. On the contrary, if the time is long and the ambient temperature is high, it is conducive to the participation of moisture in the reaction, and the curing time will be shortened accordingly.
7. Adhesive surface treatment
Removing oil, dust, paint, release agents, oxide layers and other substances that affect bonding on the surface of the bonded parts will help enhance the bonding effect of PUR hot melt adhesive.
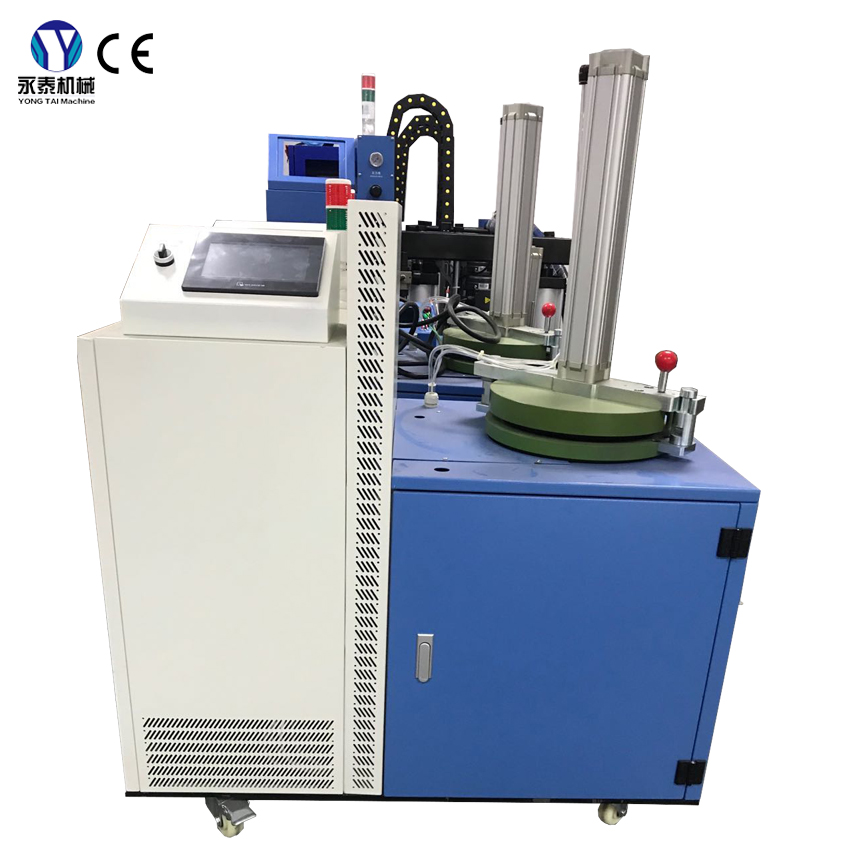